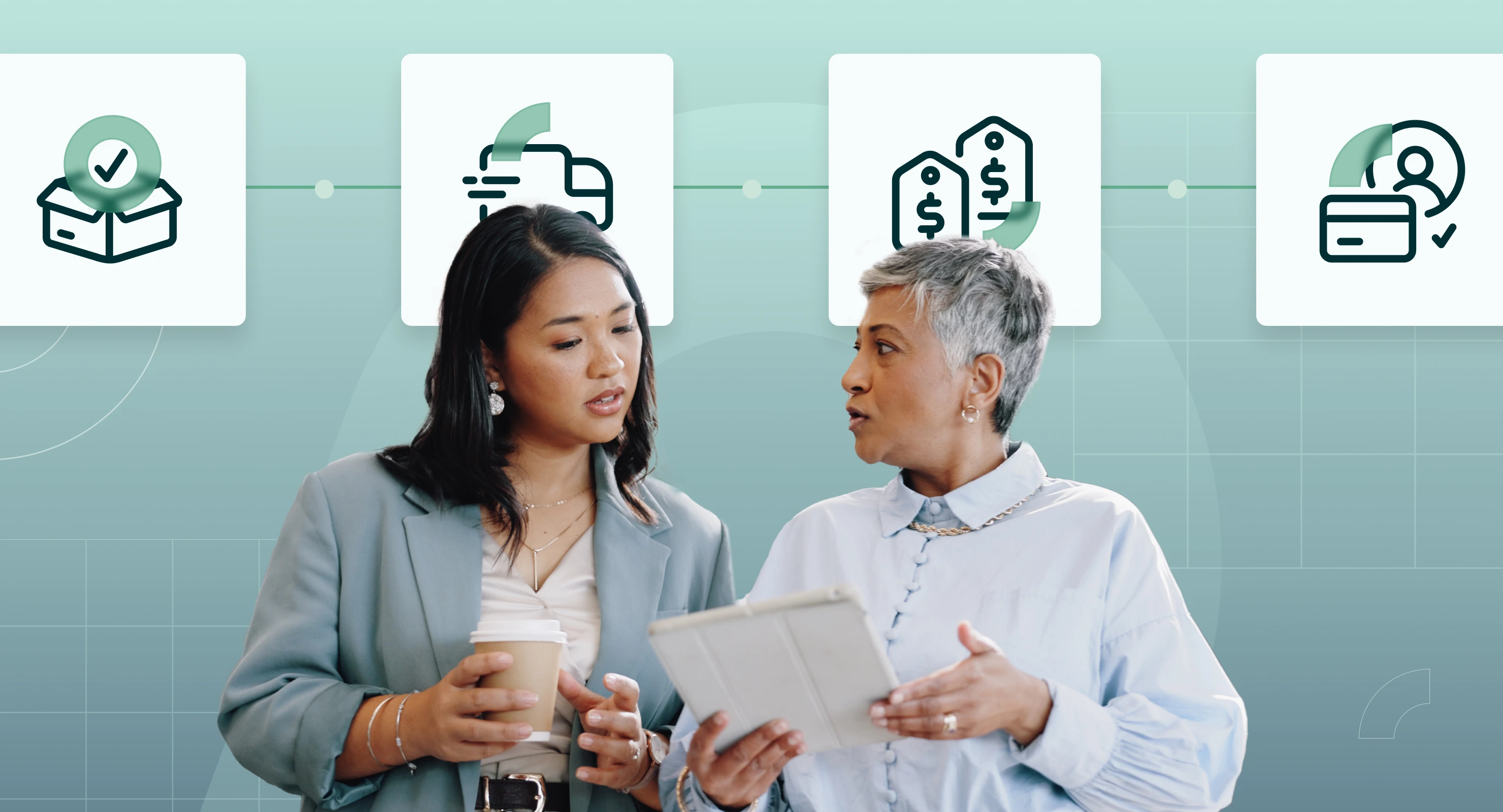
Lean vs Agile Supply Chain: A Deep Dive into Strategic Efficiency and Flexibility
Modern businesses face constant shifts in consumer demand, supply disruptions, and technological advancements.
How do they adapt?
One area of business operations that can impact growth and sustainability is through a proactive supply chain strategy. The supply chain plays a critical role in a company’s ability to stay competitive, and two of the most widely adopted methodologies are lean and agile supply chains. Each approach offers distinct advantages and caters to different business environments.
A lean supply chain focuses on efficiency, cost reduction, and minimizing waste. On the other hand, an agile supply chain emphasizes flexibility and responsiveness, particularly in industries where demand is highly variable. As the world becomes more unpredictable, many companies are adopting hybrid approaches, combining the best of both strategies. This article delves deep into the differences between lean and agile supply chains, helping you determine which one—or which combination—best suits your business needs.
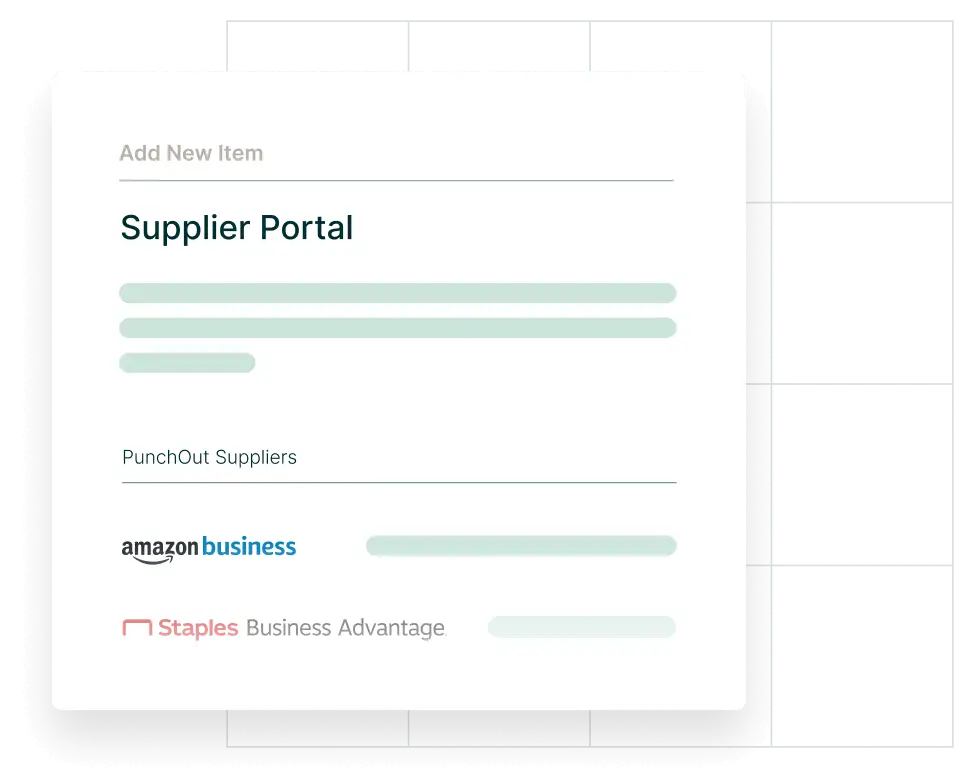
Ready to automate your vendor purchasing?
Discover how Procurify PunchOuts streamline and automate your purchasing processes with suppliers, providing accuracy to your financial data.
Section 1: What is a lean supply chain?
The lean supply chain model is built around the philosophy of operational efficiency. Originally developed by Toyota under the famous Toyota Production System, lean supply chain management focuses on reducing waste (known as Muda) and creating maximum value with minimal resources. The core idea is to eliminate anything that does not directly contribute to customer value, thereby streamlining processes and improving overall efficiency.
Key characteristics of a lean supply chain:
-
Waste elimination: Lean supply chains prioritize removing inefficiencies, whether it’s excess inventory, overproduction, or unnecessary transportation. The goal is to optimize each step in the supply chain to prevent the use of any resources that don’t add direct value to the customer.
-
Just-in-time (JIT) production: A hallmark of lean supply chain management is the Just-In-Time production system, which minimizes inventory costs by producing goods only as they are needed. This ensures that businesses don’t tie up capital in excess inventory.
-
Continuous improvement (Kaizen): Lean is not a static system; it encourages constant evaluation and improvement of processes. This commitment to Kaizen helps companies stay efficient and competitive.
-
Standardization: Lean supply chains focus on creating standardized processes to improve consistency and predictability across the entire supply chain.
Advantages of a lean supply chain:
-
Cost efficiency: By cutting out waste and reducing inventory, companies can significantly lower their operational costs and free up resources to be used elsewhere in the business.
-
Predictability: Lean supply chains work best in environments where demand is stable and predictable, allowing for tight control over production and distribution.
-
Higher quality control: With a focus on streamlining processes, Lean supply chains often lead to better quality outputs, as inefficiencies are identified and eliminated during production.
Industries & examples:
Lean supply chains are highly effective in industries where demand is predictable and operational efficiency is key. For example:
-
Automotive manufacturing (Toyota): The automotive industry has been a pioneer in lean supply chains. Toyota’s use of Just-In-Time production revolutionized manufacturing by reducing excess inventory and optimizing operational costs.
-
Consumer electronics (Apple): Apple utilizes lean strategies to ensure efficiency in production, reducing costs while maintaining high product quality.
Case study: Toyota’s lean supply chain
Toyota is perhaps the most well-known example of a lean supply chain in action. By implementing Just-In-Time production and embracing a culture of Kaizen, Toyota was able to drastically reduce waste, improve efficiency, and maintain a high level of product quality. These strategies allowed Toyota to scale efficiently, meeting customer demands while reducing unnecessary costs.
Section 2: What is an agile supply chain?
An agile supply chain prioritizes flexibility and adaptability. In an unpredictable business environment, this approach allows companies to respond quickly to changing market conditions, customer demands, or external disruptions. Unlike lean, which seeks efficiency through waste reduction, agile is designed to enable responsiveness, particularly for products with high variability or short life cycles.
Agile supply chains thrive in industries that require rapid adjustments, such as fashion, electronics, and technology. By focusing on real-time data, collaboration, and decentralized decision-making, agile supply chains can pivot and adapt to unforeseen circumstances much more effectively than traditional, rigid models.
Key characteristics of an agile supply chain:
-
Flexibility and responsiveness: Agile supply chains are built to respond quickly to fluctuations in demand or external factors such as supply disruptions or market shifts. The focus is on being able to change production or sourcing plans on short notice.
-
Real-time data usage: Agile systems often rely heavily on real-time data to inform decisions, ensuring that all parts of the supply chain can adapt simultaneously to changing conditions. This integration of technology plays a crucial role in maintaining agility.
-
Shorter lead times: Agile supply chains aim to reduce the time between receiving a customer order and fulfilling it. By reducing lead times, businesses can react faster to market trends and avoid holding excess inventory.
-
Decentralized decision-making: Agile supply chains empower teams across the network to make decisions, reducing bottlenecks and speeding up the response to changes.
Advantages of an agile supply chain:
-
Adaptability to market changes: In industries where demand is volatile, an agile approach allows companies to respond rapidly to changing customer preferences or disruptions in supply.
-
Increased customer satisfaction: Agile supply chains can adjust production based on real-time demand, ensuring that customers receive the products they need when they need them. This adaptability leads to higher customer satisfaction.
-
Reduced risk in unpredictable markets: Agile supply chains are ideal for environments that are prone to frequent shifts, such as fashion or technology, where customer demand can change overnight.
Industries & examples:
Agile supply chains are particularly suited for industries where market demand is unpredictable, or where product life cycles are short:
-
Fashion (H&M): H&M uses an agile supply chain to stay on top of fashion trends. By designing and producing clothes based on real-time demand, they minimize the risk of overproduction and excess inventory.
-
Footwear (Nike): Nike’s agile supply chain allows them to quickly respond to customer needs, particularly with customizable products like the Nike Flyknit shoes. This adaptability ensures that Nike can remain competitive in a fast-paced market.
Case study: H&M’s agile supply chain
H&M’s agile supply chain is a prime example of how adaptability can create a competitive advantage in a fast-moving industry. By leveraging a design team that works continuously on new collections and relying on short-term forecasting, H&M can respond rapidly to new fashion trends. Their supply chain adjusts quickly to produce new clothing lines and ensure they reach stores as soon as trends shift. This ability to stay in sync with customer preferences while minimizing excess inventory sets H&M apart in the fast-fashion industry.
Section 3: Lean vs agile supply chain: Key differences
While both lean and agile supply chains aim to optimize performance, they approach this goal in fundamentally different ways. Lean focuses on cost reduction and waste minimization, making it ideal for stable environments where predictability is key. Agile, on the other hand, prioritizes flexibility and adaptability, thriving in markets with high demand variability and shorter product life cycles. Below is a detailed comparison of the two methodologies to help you better understand their key differences.
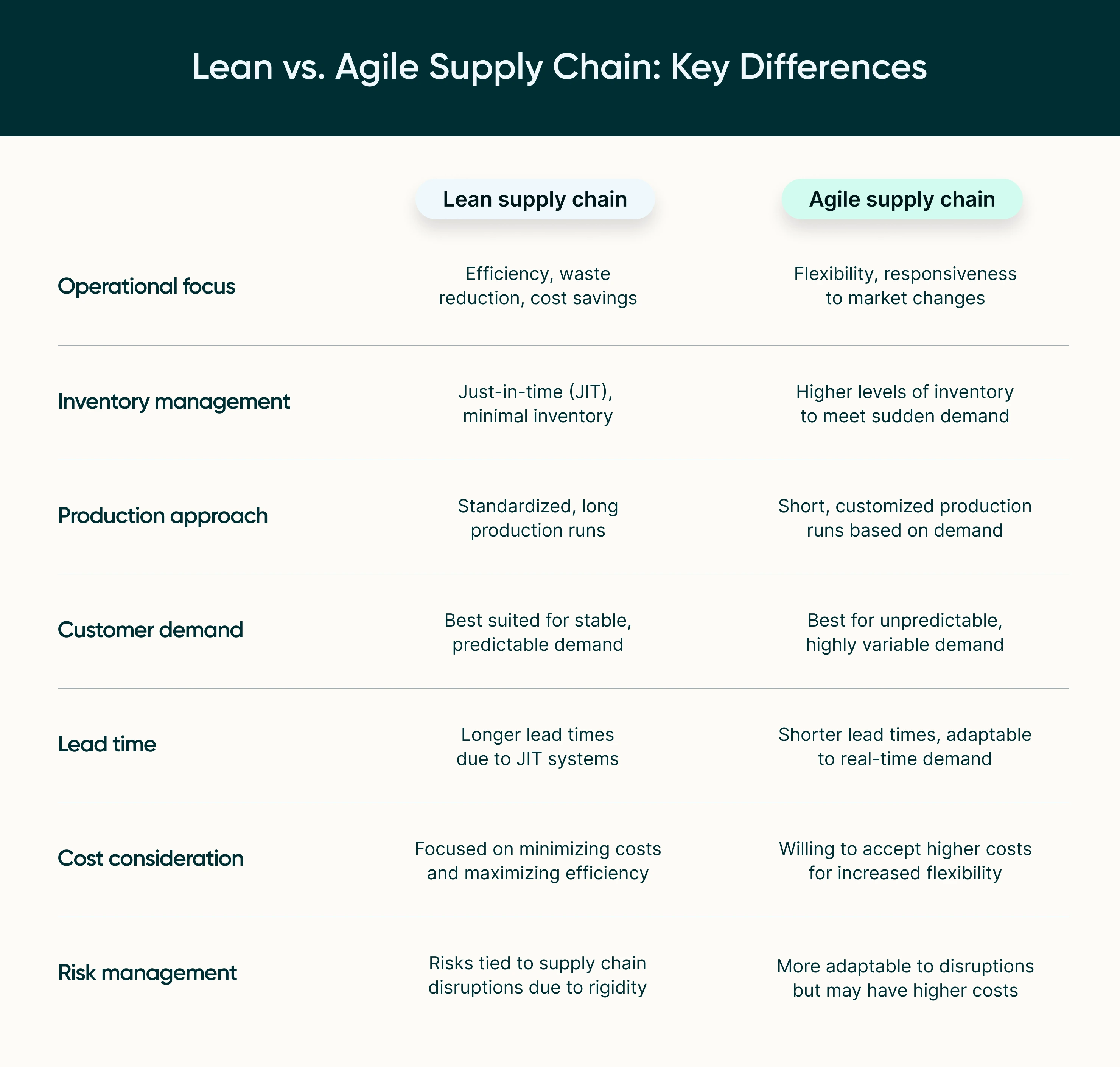
Operational focus: Efficiency vs. flexibility
The primary difference between lean and agile supply chains lies in their focus. A lean supply chain emphasizes efficiency by reducing waste and streamlining operations. Lean companies aim to create maximum value using minimal resources, focusing on predictable, stable demand.
On the other hand, agile supply chains focus on flexibility and responsiveness. In environments where demand is unpredictable or prone to rapid changes, agile companies prioritize the ability to pivot quickly, even at the cost of higher operational expenses.
Inventory management: Minimal vs. strategic inventory
Lean supply chains aim to reduce inventory to an absolute minimum. By employing Just-in-Time (JIT) principles, lean companies only produce goods when they are needed, reducing storage and inventory costs.
However, this approach can make lean supply chains vulnerable to disruptions if demand suddenly spikes or suppliers encounter delays.
In contrast, agile supply chains often keep higher levels of strategic inventory to accommodate unexpected changes in demand. This allows agile companies to meet customer needs more quickly, even if it results in higher carrying costs.
Production approach: Standardization vs. customization
Lean supply chains emphasize standardization, with long production runs that maximize efficiency. This approach works best in industries where products are highly standardized, such as automotive manufacturing.
Agile supply chains, on the other hand, embrace shorter, more flexible production runs. Companies that produce customized or fast-changing products—such as those in the fashion or technology industries—benefit from the adaptability of an agile approach.
Customer demand: Predictability vs. variability
Lean supply chains are best suited for industries with stable and predictable demand. Since lean systems rely on accurate forecasting and JIT production, they perform well in markets where customer demand doesn’t fluctuate significantly.
In contrast, agile supply chains are designed to handle industries with highly variable demand. This adaptability allows companies to respond to sudden changes in consumer preferences or market conditions, making agile the preferred choice for sectors like fashion or consumer electronics.
Lead times: Longer vs. shorter
Lean supply chains, with their emphasis on JIT production, often have longer lead times because goods are only produced or delivered when needed. This reduces inventory but can slow down the supply chain if demand unexpectedly increases.
Agile supply chains, however, prioritize shorter lead times. By keeping some inventory on hand and adapting production quickly, they can fulfill orders faster and meet real-time demand more effectively.
Cost considerations: Efficiency vs. adaptability
Lean supply chains are typically more cost-efficient because of their focus on eliminating waste and optimizing every step of the process. However, this emphasis on efficiency can make them less flexible.
Agile supply chains, while more adaptable, often incur higher operational costs due to their need for additional inventory, faster production cycles, and real-time responsiveness. Companies using agile methods accept these costs as the trade-off for greater flexibility in meeting customer demands.
Risk management: Rigid vs. resilient
Lean supply chains can be more vulnerable to risks, such as supply chain disruptions, because their minimal inventory levels and rigid processes leave little room for error.Any delay or disruption can lead to significant bottlenecks, affecting production and customer satisfaction.
Agile supply chains are more resilient to disruptions. They can pivot quickly when faced with external challenges, such as supplier issues or sudden demand changes. However, this flexibility comes at the expense of higher costs.
Section 4: When to choose lean or agile for your supply chain
Selecting the right supply chain strategy depends on several factors, including the nature of your products, market demand, company goals, and the industry in which you operate. Both lean and agile supply chains offer distinct advantages, but they cater to different environments. In some cases, businesses may find that a hybrid approach combining both strategies provides the best solution.
Product type: Standardized vs. customizable
If your product offerings are standardized and do not require frequent changes, a lean supply chain is typically the best choice. Lean excels in industries where demand is stable and predictable, such as automotive manufacturing or consumer electronics, where companies can plan long production runs without the risk of obsolescence.
On the other hand, if your products are highly customizable or have short life cycles, an agile supply chain is more appropriate. Industries like fashion, consumer technology, and sportswear (e.g., Nike’s customizable Flyknit shoes) benefit from Agile methods because they allow businesses to adapt quickly to changing trends and customer demands.
Demand predictability: Stable vs. volatile
The level of demand predictability plays a critical role in choosing between lean and agile supply chains. For businesses with stable, predictable demand, a lean strategy allows for efficient operations with minimal waste and lower costs. For example, Apple’s lean supply chain model is well-suited for its consistent production needs.
However, in industries where demand is more volatile and unpredictable, such as fast fashion or consumer electronics, an agile supply chain offers the flexibility to respond to sudden changes. Companies like H&M or Zara use agile practices to adjust their supply chains in real time, ensuring they can meet fluctuating consumer preferences.
Market conditions: Stable vs. dynamic
In industries with stable market conditions, lean supply chains thrive because of their focus on cost efficiency. lean is ideal for businesses that operate in markets where disruptions are rare, and product demand is consistent. This allows for tighter control over production schedules and minimal inventory.
Conversely, in dynamic and rapidly changing markets, such as technology or retail, an agile supply chain is essential. These businesses must be able to pivot quickly to meet new customer demands or adapt to changes in market conditions.
For example, the COVID-19 pandemic highlighted the need for agile supply chains, as companies with more flexible systems were able to adapt to sudden disruptions more effectively.
Supply chain complexity: Simple vs. complex
The complexity of your supply chain also influences the choice between lean and agile strategies. A lean approach works best when the supply chain is relatively simple and the company has tight control over its suppliers, production, and distribution. In such cases, the focus is on optimizing efficiency by reducing waste at every step.
However, for more complex supply chains that involve multiple suppliers, unpredictable lead times, or customized products, an agile supply chain is better suited. Agile systems are designed to handle higher levels of complexity, allowing for more decentralized decision-making and faster responses to changes.
Scalability & flexibility needs
If your business is scaling rapidly, flexibility becomes crucial, and an agile supply chain will offer the ability to adjust to new volumes and new markets more easily. Agile supply chains allow for real-time data usage, so scaling businesses can make faster decisions and pivot when necessary.
In contrast, for established companies with stable demand, a lean supply chain offers the cost benefits of efficiency, making it a more suitable choice for maintaining consistent performance at a large scale.
Hybrid approach: Best of both worlds
For many businesses, the ideal solution lies somewhere between lean and agile. A hybrid supply chain can combine the cost-efficiency of lean for standardized products and the flexibility of agile for high-variability products. Companies like Zara exemplify this approach, applying lean principles to predictable products and Agile principles to less predictable or customizable offerings.
Case study: Zara’s hybrid model
Zara, a global fast-fashion retailer, has successfully implemented a hybrid approach by using lean principles for standardized products and agile methods for products that are trend-driven. By delaying the final stages of production (e.g., dyeing or adding finishing touches) until they have a clearer understanding of demand, Zara combines the efficiency of lean with the responsiveness of agile. This allows them to minimize waste while ensuring they can adapt quickly to changing fashion trends.
Section 5: Hybrid supply chain models
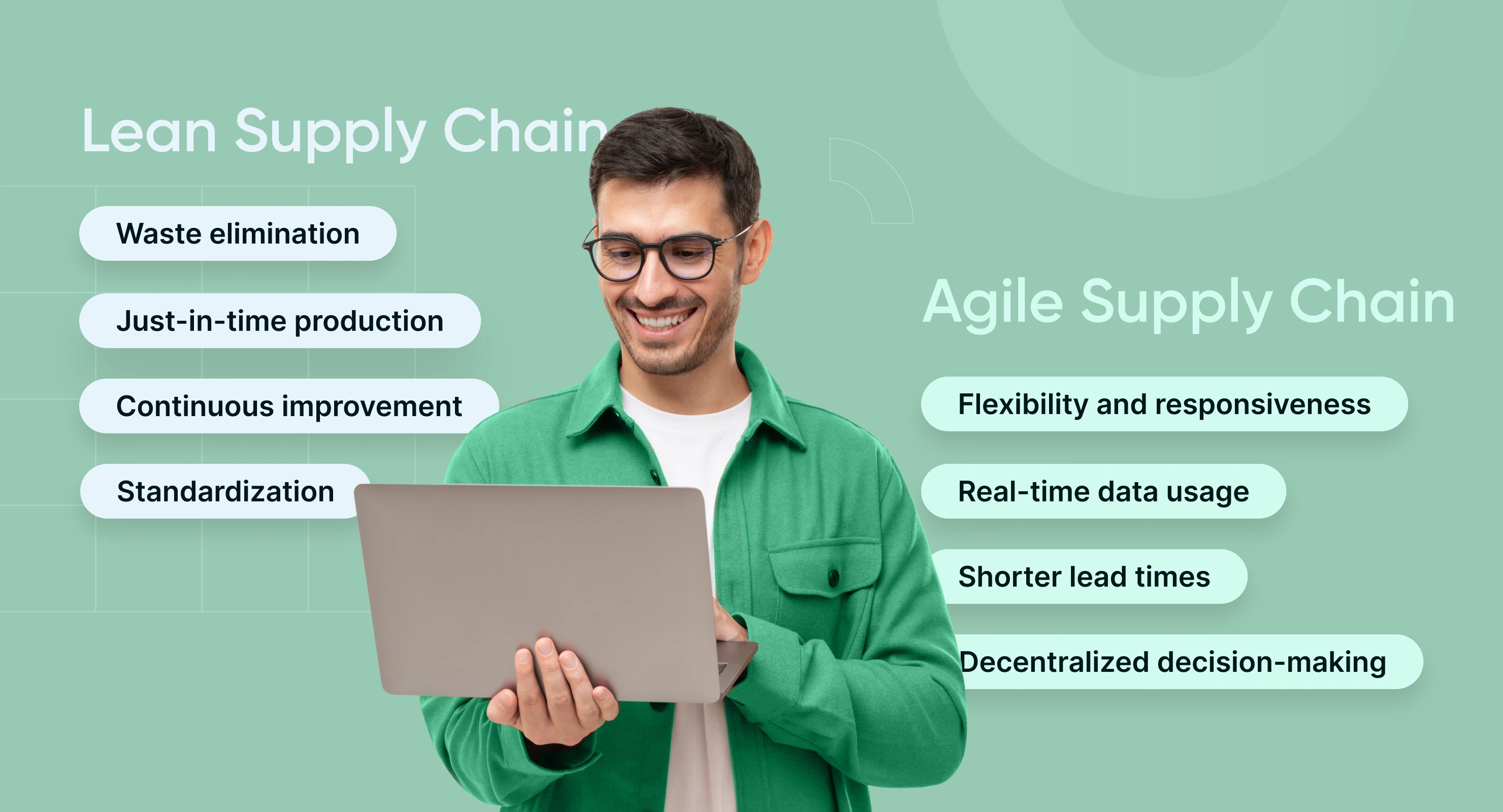
In today’s fast-evolving business landscape, many companies are finding that neither a purely lean nor a purely agile supply chain is the perfect fit. Instead, they are adopting hybrid supply chain models that combine the strengths of both approaches. By blending the efficiency of lean with the flexibility of agile, businesses can create supply chains that are both cost-effective and adaptable to changing market conditions.
Hybrid supply chains allow companies to take advantage of lean principles where demand is predictable and efficiency is paramount, while leveraging agile strategies in areas where demand is more variable and customer needs can shift rapidly. This balance provides a more robust, resilient supply chain capable of thriving in diverse market conditions.
Key benefits of a hybrid supply chain:
-
Cost efficiency with flexibility: A hybrid model allows businesses to benefit from the cost-saving efficiency of lean supply chains while still maintaining the flexibility to adapt to market changes using agile principles. This balance enables companies to reduce waste in stable parts of their supply chain while being responsive to unpredictable areas.
-
Risk mitigation: By incorporating agile elements, businesses can better manage risks related to supply chain disruptions. While lean systems can be vulnerable to external shocks, agile practices enable quicker responses to sudden changes.
-
Scalability and adaptability: Hybrid supply chains are scalable, allowing companies to adapt to growth or new market conditions without overhauling their entire operation. This makes hybrid models particularly valuable for businesses that experience both steady, long-term demand and sudden spikes due to new product launches or promotions.
Examples of hybrid supply chains:
-
Zara (fashion industry): As mentioned earlier, Zara uses a hybrid approach by applying lean principles to predictable product lines and agile methods to trend-driven items. This allows them to react quickly to changes in fashion while keeping costs low for more stable product lines.
-
Kimberly-Clark (consumer goods): Kimberly-Clark, the company behind brands like Kleenex and Huggies, uses a hybrid supply chain strategy. For their everyday, standardized products, they employ lean methods to ensure efficiency. However, when promoting new products or responding to demand spikes, they adopt agile practices to stay responsive.
Challenges of hybrid supply chains:
While hybrid models offer significant benefits, they also come with challenges. The primary challenge is the increased complexity in managing two different strategies within the same supply chain. Companies must carefully decide which parts of their operation require lean efficiency and which parts demand agile flexibility. Balancing these approaches without creating bottlenecks or inefficiencies requires strong supply chain management and clear communication across teams.
How to Implement a hybrid supply chain:
-
Segmentation: Segment your product portfolio based on demand predictability. Products with stable demand can follow lean practices, while products with volatile demand can adopt agile strategies.
-
Technology integration: Use supply chain management software that provides real-time data and analytics. This will help you maintain agility while optimizing lean operations through better inventory management, demand forecasting, and supply chain visibility.
-
Collaboration across teams: Ensure that all teams within your supply chain—procurement, manufacturing, logistics—are aligned. Strong collaboration is necessary to ensure that the lean and agile elements of your supply chain work seamlessly together.
Section 6: The future of supply chain strategies: Lean, agile, or hybrid?
As businesses continue to evolve and face new challenges, the future of supply chain management will be shaped by advances in technology, changing consumer expectations, and global market dynamics. Companies are increasingly adopting digital tools, automation, and data-driven strategies to enhance their supply chain operations. As a result, the debate between lean and agile supply chains is shifting toward a more hybrid, technology-integrated future.
The role of technology in future supply chains
The integration of advanced technologies like artificial intelligence (AI), machine learning, blockchain, and Internet of Things (IoT) is transforming how supply chains are managed. These tools allow companies to gather real-time data, optimize decision-making, and increase visibility across the entire supply chain.
With AI-powered analytics, businesses can more accurately forecast demand, improve inventory management, and automate routine tasks, making both lean and agile supply chains more efficient and responsive.
-
Automation: Automation in manufacturing, warehousing, and logistics will further streamline lean supply chains, reducing human error and enhancing efficiency. In agile systems, automation enables faster response times and greater adaptability, as businesses can pivot quickly when disruptions occur.
-
Blockchain for transparency: Blockchain technology enhances transparency and traceability in the supply chain, allowing for real-time tracking of goods, reducing fraud, and improving communication between suppliers, manufacturers, and customers.
Customer-centric supply chains
In the future, supply chains will need to become even more customer-centric. The rise of e-commerce and on-demand services has raised consumer expectations for faster, more flexible deliveries. This shift is pushing businesses to adopt agile practices to meet the growing demand for customization, speed, and transparency.
Companies that cannot quickly respond to these new customer expectations may fall behind their competitors.
Resilience and risk management
The COVID-19 pandemic underscored the importance of having a resilient supply chain. In the future, companies will need to build supply chains that can withstand disruptions—whether from global pandemics, natural disasters, or geopolitical events. Businesses are increasingly combining lean cost-efficiency with agile flexibility to create more resilient supply chains.
By diversifying suppliers and using real-time data to predict potential disruptions, companies can create a more robust framework that balances efficiency with adaptability.
Hybrid models: The new norm
As companies strive to be both efficient and flexible, hybrid supply chains are likely to become the standard model for many industries. By leveraging the best elements of both lean and agile methodologies, businesses can adapt their supply chain strategies based on product types, market conditions, and consumer demands. For instance, companies like Zara and Kimberly-Clark will continue to refine their hybrid models, combining lean practices for predictable products and agile practices for trend-driven or new product lines.
Trends to watch:
-
Sustainability: Increasingly, companies are incorporating sustainability into their supply chain strategies. As consumer demand for eco-friendly products grows, lean supply chains’ focus on waste reduction aligns well with sustainability goals. Meanwhile, agile practices can help companies quickly adjust to new environmental regulations and sustainable sourcing.
-
AI and predictive analytics: AI-powered predictive analytics will become even more central to supply chain management. Companies using these tools will have a significant competitive advantage, as they can more accurately predict market trends and customer demands.
-
Localization: The trend toward localized supply chains—where companies shift away from long-distance global sourcing to more regional supply chains—will continue to grow. This shift, driven by both geopolitical tensions and the need for faster lead times, can benefit both lean and agile systems depending on the region and industry.
Conclusion
The future of supply chain management is no longer a simple choice between lean or agile. As businesses navigate increasingly complex and unpredictable markets, hybrid models that combine the best of both approaches are becoming the norm. By leveraging cutting-edge technologies and maintaining a customer-centric focus, companies can build supply chains that are efficient, flexible, and resilient enough to meet the challenges of tomorrow.