Procure to pay KPIs: 11 metrics you need to track
Many established companies use Key Performance Indicators (KPIs) as a way to measure the success of a particular activity that it is engaged in. The Procure-to-Pay cycle is an important component to many businesses, and establishing a measure of its success is essential.
The data collected from tracking KPIs will give you insight into your company’s performance and operations and help you make informed business decisions. According to a recent survey, 78 percent of CPOs say that cost reduction is a priority for their procurement strategy. These KPIs can help organizations optimize resources, spending, time, and costs.
Procurement KPIs you need to track
1. Cost per invoice
The cost per invoice is measured based on the amount of time an employee spends drafting an invoice. The cost per invoice includes things such as personnel, IT, administration, printing, mailing, etc. Automation will greatly improve the efficiency of the procure-to-pay cycle, reduce costs and help prevent errors.
2. First-time match rate
First-time match rate (FTM) is the measure used to determine the accuracy of the three-way matching process. Three-way matching is based on the concept of verifying three critical documents: the invoice, the purchase order and the receiving documents. Many companies hover at a first-time match rate of about 70 to 90 percent, while lower performing companies, typically, drop below a 50 percent match rate.
3. Productivity per FTE (Full-time employee)
In order to track cost reductions in the procurement process, managers must be able to measure the productivity per full-time equivalent employee (PPFTE). PPFTE is based on a simple 0-1 scale, where 0.5 represents a part time employee, and 1 represents a full-time employee. PPFTE will allow a company to quantify larger processes, based on the total number of FTEs required to complete a specific task.
4. Spend under management
Spend Under Management (SUM) measures the percentage of total spend that falls under management’s responsibility. However, measuring SUM is only possible with an IT solution in place that tracks invoice processing. Once that IT solution is in place, there is a host of criteria that needs to be met when tracking SUM. For example, to be considered when analyzing SUM, purchases must meet the following criteria:
- Be from an approved supplier
- Purchase was properly authorized
- Paid on correct terms and pricing
- Transactions are clearly visible and approved by management
5. Payments on time
This procurement KPI measures the percentage of invoices that you pay your suppliers on time. On time payment requires close collaboration between procurement and finance. This ensures that bills are paid at the right time to maintain optimal cash flow. Paying your bills on time will also help strengthen your supplier relationships.
6. Invoice processing time
Invoice processing time considers how long it takes for an invoice to be processed from receiving the invoice to approval and verification to payment. This measure is a good indication of how efficient your accounts payable department is.
7. Number of suppliers per 1,000 invoices
Take a look at how many suppliers you receive invoices from. It’s usually more manageable to have a slim list of suppliers that you know very well and work with every day. If you work with a lot of suppliers, it might be worth taking the time to do some supply base optimization.
8. Supplier lead time
Supplier lead time refers to the number of days between the time a supplier receives an order and when the order is shipped. This measure is critical so you know when you can expect to receive the goods or services that you ordered. For example, if you need something urgently, you might choose to go with a supplier that has a shorter lead time.
9. Percentage of contactless invoices
Contactless or touch less invoices refer to the number of invoices that don’t require human intervention. Generally, these invoices match the first time, the information is correct, and the automation tools are working properly. This is a good measure of efficiency.
10. Duplicate payment and invoices rate
This KPI is a good litmus test for how error-prone your accounting system is. There are many reasons why duplicate invoices and payments may occur. Sometimes, these may seem like small errors, but they add up over time and slow down processing time and they may even result in larger errors. Again, automation can help reduce duplicates and errors.
11. Supplier defect rate
This is a measure used to assess the quality of a supplier’s products or services. It’s the percentage of materials that don’t meet quality standards. This KPI will also give you insight into the supplier’s operations and trustworthiness.
Procurement KPIs: the key to unlocking efficiency
These suggestions, of course, are only a few ways your purchasing and accounting departments can improve your procure-to-pay cycle. Tracking these procurement KPIs will allow you to identify what your organization is doing well and areas for improvement. The data collected will help you understand your own procure-to-pay cycle in more detail, reduce costs, and improve efficiency.
Editor's note Original publish date: 13 March 2013 Original author: Kenneth Loi We've since updated and republished this blog post with new content.
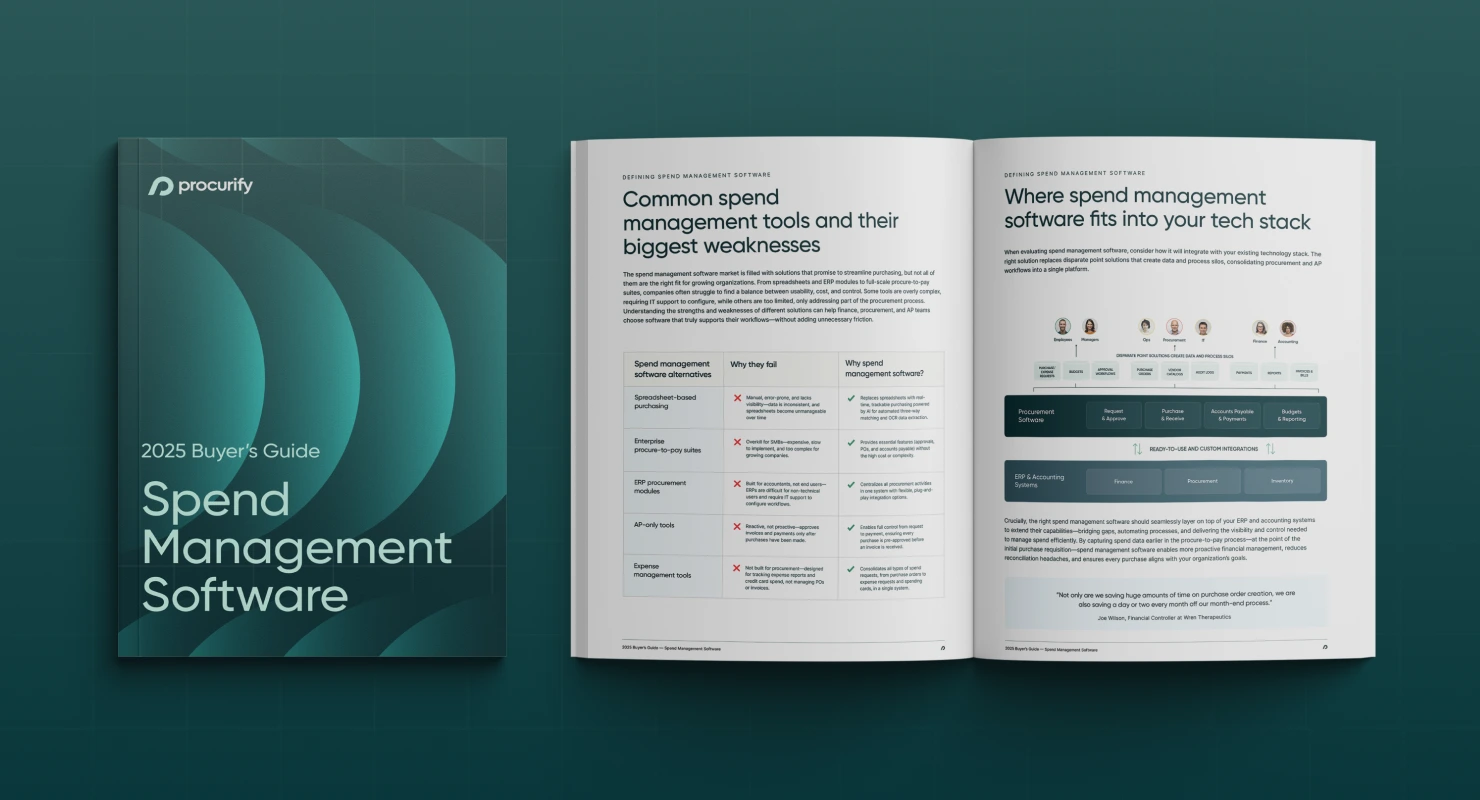
2025 Spend Management Software Buyer’s Guide
Choose the spend management solution best suited to your organization’s needs with an overview of the 2025 software ecosystem, feature comparisons, and a free vendor capability evaluation checklist.